Технология переработки нефти и газа. Часть 1Промышленное оформление гидрогенизационных процессов.
В технологических схемах различных гидрогенизационных процессов много общих черт. В них можно выделить следующие общие элементы (рисунок 4.8). Сырье перед нагревом в теплообменном и печном оборудовании смешивается с водородсодержащим газом в тройнике смешения. После выхода из печи газосырьевая смесь (ГСС) направляется в реакторный блок (мо-жет состоять из одного или нескольких реакторов), в котором осуществляют-ся все химические превращения. В зависимости от глубины превращения сырья может изменяться суммарный тепловой эффект реакций. Поэтому в неко-торых процесса х, частности при гидро крекинге, требуется промежуточное охлаждение продуктовой смеси, что достигается подачей холодного ВСГ (квенча) или в реактор полочного типа, или в трубопровод, соединяющий ре-акторы.
После выхода из реактора газопродуктовый поток (ГПП) охлаждается в теплообменном оборудовании и затем подвергается сепарации. При этом могут использоваться две технологии: холодная или горячая сепарации. Выде-ляемые в блоке сепарации ВСГ и углеводородный газ направляются на мо-нометаноламиновую (МЭА) очистку от сероводорода, а жидкие углеводоро-ды – на ректификацию.
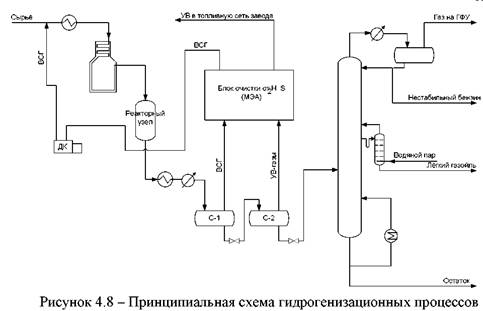
Принцип работы блоков сепарации по схеме холодной и горячей сепа-рации приведен на рисунке 4.9. По первому варианту ГПП охлаждается в те-плообменном и холодильном оборудовании ориентировочно до 40°С и при давлении на 0,2-0,5 МПа ниже, чем на выходе из последнего реактора, под-вергается разделению на газообразную и жидкую фазы в сепараторе высоко-го давления. Газообразная фаза – ВСГ, возвращается в процесс, жидкая фаза после сброса давления поступает в сепаратор низкого давления, где из нее выделяются углеводородные газы, направляемые после очистки или в топ-ливную сеть завода, или на газофракционирование. Давление в сепараторе низкого давления обычно составляет 0,8-1,2 МПа.
При горячей сепарации ГПП после выхода из реактора охлаждается в теплообменном оборудовании примерно до 200-245°С и при высоком давле-нии и температуре подвергается разделению в горячем сепараторе. Газооб-разная фаза – смесь ВСГ, газов С1-С4 и более тяжелых углеводородов, охла-ждается в воздушных и водяных холодильниках до 40°С и при высоком дав-лении поступает в холодный сепаратор, где из нее конденсируются тяжелые углеводороды. Несконденсированная газовая фаза представляет собой ВСГ. Он возвращается в процесс, а жидкие фазы из горячего и холодного сепара-торов направляются на ректификацию. На некоторых заводах при горячей сепарации продуктов гидрогенизационных процессов используют еще один горячий сепаратор, в который поступает
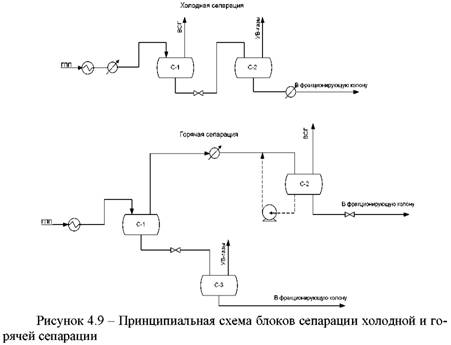
жидкая фаза из горячего сепаратора высокого давления (рисунок 4.9). В нем за счет сброса давления происходит выделение легких углеводородов. Пре-имуществом горячей сепарац ии по сравнению с холодной являются более низкие энергетические затраты на ведение процесса, за счет исключения ста-дии охлаждения и последующего нагрева части продуктового потока перед его ректификацией. Недостатком же ее считается более низкая концентрация выделяемого циркулирующего ВСГ. По этой причине в процессах, в которых требуется высокая концентрация водорода в ВСГ (гидрокрекинг, каталитиче-ская гидродепарафинизация), используется только холодная сепарация.
Реакторный блок состоит обычно из 1-3 реакторов. При двух и более реакторах в блоке они могут быть включены в схему последовательно или параллельно (рисунок 4.10).
Следует помнить, что при параллельном подключении реакторов необ-ходимо обеспечить хорошее перемешивание газосырьвой смеси перед ее раз-ветвлением на два потока. Это позволит предотвратить неравномерное рас-пределение по реакторам жидкой фазы и ускоренное закоксовывание катали-затора в одном из них.
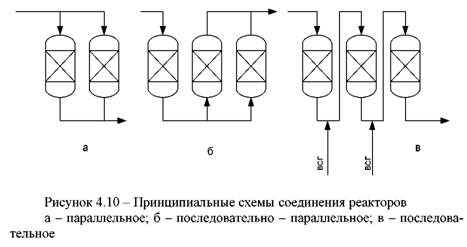
Описание технологической схемы секции гидроочистки дизельной фракции (на примере схемы секции 300/1 установки ЛК-6У)
В 1992 году секция 300/1 установки ЛК-6У №2 реконструирована для перехода на метод горячей сепарации. В 2001 году проведена модернизация реакторного блока с монтажом двух дополнительных параллельно работаю-щих реакторов Р-303/1, Р-303/2, которые установлены после реактора Р-301 с целью получения дизельного топлива, соответствующего перспективным ев-ропейским стандартам. Технологическая схема м одернизированной секции приведена на рисунке 4.11.
Сырье – широкая дизельная фракция 180-360°С из резервуаров P-59,60 или Р-49,50 промпарков ЛК-бУ № 1,2, поступает на прием подпорного насоса Н-310 (Н-310а) и подается в теплообменник Т-306, где нагревается теплом гидроочищенной фракции, выходящей снизу колонны К-301 до 120–160°С и поступает на прием сырьевых насосов H-301–303,303а. Эти насосы подают его в тройник смешения, куда поступает циркулирующий водородсодержа-щий газ (ВСГ) от компрессора ЦК-301. Расход сырья обычно составляет 130– 320 м3/час. Есть возможность приема прямогонного дизельного топлива по “жесткой схеме” из секции 100 на прием подпорного насоса Н-310(310а). По-сле смешения газосырьевая смесь (ГСС) с температурой до 120–160°С по-ступает в межтрубное пространство сырьевых теплообменников T-30I–303, где нагревается до 280–300°С. Далее ГСС поступает в печь П-301/1,2, где на-гревается до 340–400°С и поступает в реактор Р-301, где на катализаторе при давлении на входе 5,0 МПа (изб) и температуре 330-390°С
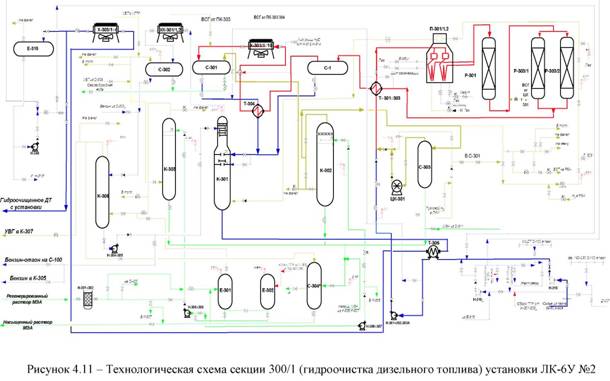
проходят реакции гидрирования серо- и азотсодержащих соединений (в большей степени), реакции гидрирования олефинов и полициклических со-единений (частично). Процесс гидроочистки в реакторе Р-301 протекает с выделением тепла, поэтому для поддержания требуемой температуры на входе в реакторы Р-303/1 и Р-303/2 предусмотрена подача водородсодержа-щего газа от компрессора ЦК-301 (квенч) в трубопровод на выходе из реак-тора Р-301. Газопродуктовая смесь (ГПС) после реакторов Р-303/1,2 объеди-няется и поступает в трубное пространство теплообменников Т-303–301, где охлаждается потоком ГСС и далее направляется в горячий сепаратор С-1. Часть потока ГПС после реакторов Р-303/1,2 поступает помимо теплообменников T-303–301 сразу в сепаратор C-1 для регулирования темпе-ратуры гидрогенизата. В горячем сепараторе С-1 поток ГПС разделяется на нестабильный гидрогенизат и парогазовую фазу, часть которой поступает в трубное пространство теплообменника Т-304, где отдает тепло потоку неста-бильного гидрогенизата из сепаратора C-301, затем охлаждается в воздуш-ном холодильнике X-301 до 20–55°С и входит в сепаратор C-301. Перед воз-душным холодильником в поток газопродуктовой смеси подается химочи-щенная вода от насосов Н-31З, 314 для связывания и удаления аммиака, ко-торый образует соли аммония, вызывающие коррозию оборудования, из цир-кулирующего ВСГ.
Забиваем Сайты В ТОП КУВАЛДОЙ - Уникальные возможности от SeoHammer
Каждая ссылка анализируется по трем пакетам оценки: SEO, Трафик и SMM.
SeoHammer делает продвижение сайта прозрачным и простым занятием.
Ссылки, вечные ссылки, статьи, упоминания, пресс-релизы - используйте по максимуму потенциал SeoHammer для продвижения вашего сайта.
Что умеет делать SeoHammer
— Продвижение в один клик, интеллектуальный подбор запросов, покупка самых лучших ссылок с высокой степенью качества у лучших бирж ссылок.
— Регулярная проверка качества ссылок по более чем 100 показателям и ежедневный пересчет показателей качества проекта.
— Все известные форматы ссылок: арендные ссылки, вечные ссылки, публикации (упоминания, мнения, отзывы, статьи, пресс-релизы).
— SeoHammer покажет, где рост или падение, а также запросы, на которые нужно обратить внимание.
SeoHammer еще предоставляет технологию Буст, она ускоряет продвижение в десятки раз,
а первые результаты появляются уже в течение первых 7 дней.
Зарегистрироваться и Начать продвижение
В сепараторе C-301 происходит разделение потока газопродуктовой смеси на нестабильный гидрогенизат, воду и циркуляционный газ. Циркуля-ционный газ направляется в абсорбер К-302, где очищается от сероводорода раствором МЭА. Очищенный ВСГ из абсорбера К-302 через сепаратор С-303 поступает на прием циркуляционного компрессора ЦК-301, который подает его в тройник смешения. Для компенсации израсходованного водорода и поддержания необходимого парциального давления водорода циркуляцион-ный газ смешивается со свежим ВСГ, поступающим от компрессоров ПК-303, 304, в сепаратор С-301 или в линию нагнетания компрессора ЦК-301. Жидкость (р-р МЭА) из сепаратора С-303 сбрасывается периодиче-ски в сепаратор насыщенного МЭА С-304а. Горячий нестабильный гидроге-низат из сепаратора C-I и нагретый в теплообменнике Т-304 нестабильный гидрогенизат из сепаратора C-301 объединяются и с температурой 210–250°С поступают в стабилизационную колонну K-301.
Вниз колонны K-301 подается водородсодержащий газ со щита сдува секции 300/1 или с установки PSA, который подогревается в газоподогрева-теле, установленном в газоходах печи П-301/1,2. Подача ВСГ, выполняющего функцию испаряющего агента, приводит к понижению парциального давле-ния паров нефтепродуктов в колонне и облегчает испарение жидкого остатка. Щит сдува позволяет также сбрасывать ВСГ из реакторного блока секции 300/I в топливную сеть или на факел. Пары воды, бензина и углеводородный газ выводятся сверху колонны К-301 с температурой 150–200°С, проходят конденсатор-холодильник XK-301, где охлаждаются до температуры не бо-лее 50°С и поступают в сепаратор С-302, в котором происходит отделение газа от жидкости и разделение бензина и воды.
Бензин из сепаратора С-302 поступает в колонну К-308 для очистки от сероводорода очищенным углеводородным газом из абсорбера К-303, откуда он насосами Н-304,305 частично подается на орошение колонны К-301; ба-лансовое количество бензина выводят с установки. Имеется перемычка из линии гидроочищенного дизтоплива в линию орошения колонны K-301 для регулирования температуры вверху К-30I при аварии насосов Н-304,305. Бензин из сепаратора С-302 выводится в этом случае в неконди-цию по байпасу колонны К-308.
Избыточный бензин может выводиться:
в сырье колонны К-305 секции 300/2 при работе установки для производства реактивного топлива;
через линию некондиции на прием сырьевых насосов секции 100.
Вода из сепаратора С-302 периодически выводится в линию кислой воды с установки. Углеводородный газ из сепаратора С-302 поступает в аб-сорбер К-303, куда подается газ из сепаратора С-309 секции 300/2 и углево-дородный газ с УЛГК (установки легкого гидрокрекинга), где они очищают-ся от сероводорода раствором МЭА. Раствор МЭА подается в абсорбер К-303 из емкости E-30I насосами Н-308, 309. При давлении
0,8–1,0 МПа в коллекторе регенерированного МЭА, поступающего с установки серы, насосы Н-308,309 можно не включать, а подавать его за счет давления в коллекторе. Часть углеводородного газа из абсорбера К-303 на-правляется в колонну К-308. Предусмотрена возможность сброса углеводо-родного газа из сепаратора С-302 помимо абсорбера К-303 в топливную сеть или на факел. Из колонны К-308 газ также можно вывести на факел.
Стабильная гидроочищенная фракция уходит снизу колонны K-301, охлаждается последовательно в теплообменнике Т-306 (межтрубное про-странство), воздушном холодильнике Х-303 и поступает в емкость E-315, где происходит ее дополнительная сепарация. При необходимости гидроочи-щенное топливо после воздушного холодильника Х-303 можно сразу вывести на ТСБ. Газ, выделяюшийся в емкости E-315, выводится на факел, а дизель-ное топливо поступает на прием насосов Н-340 (310а) и откачивается на ТСБ.
Раствор МЭА из емкости E-301 насосами Н-306,307 подается в абсор-бер К-302 и абсорбер К-306, а насосами Н-308,309 в абсорбер К-303. В аб-сорбер К-307 раствор МЭА подается за счет давления в коллекторе регенери-рованного МЭА. Насосы Н-308, 309 используются также для откачки раство-ра МЭА из емкостей E-30I, 302 в период подготовки к ремонту. Насыщенный МЭА из К-302,303,306,307 подается в сепаратор С-304а, где происходит вы-деление газа и отделение жидких углеводородов от МЭА. В сепаратор С-304а также выводится раствор МЭА из сепараторов С-303,311. Раствор МЭА из сепаратора С-304а подается на установку регенерации МЭА. Нефтепродукт периодически дренируется вручную в емкость Д-207. Углеводородный газ из сепаратора С-304а поступает в колонну К-307 на очистку от сероводорода.
Все параметры технологического режима установки выведены на щит в операторной и на монитор ПЭВМ секции 300/1.
|