Технология термической обработки металловЦементация в твердом карбюризаторе
и в течение длительного времени выдерживают при этой температуре, затем охлаждают и подвергают термической обработке.

При контакте со стальными деталями окись углерода разлагается на двуокись углерода и атомарный углерод:

Атомарный углерод адсорбируется поверхностью детали и диффундирует в сталь, растворяясь в у-фазе:

Если атомарный углерод образуется в большом количестве (больше, чем может продиффундировать в сталь), то он превращается в молекулярной и отлагается на поверхности детали в виде сажи.
(в количестве 10—25%) При добавлении этих солей протекают реакции:
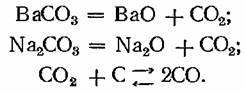

Углекислый натрий в начале процесса цементации действует энергично в связи с тем, что в начальной стадии цементации в ящике содержится до 50% СО и выше; далее содержание окиси углерода понижается и активность углекислого натрия постепенно ослабляется.
могут быть
в количестве
отличающегося большой реакционной способностью. Применение в качестве активизаторов ацетатов позволяет заменить часть древесного угля более теплопроводным и имеющим меньшую усадку каменноугольным полукоксом.

добавляют для предотвращения спекания карбюризатора.
При использовании в качестве активизаторов ацетата натрия и ацетата бария рекомендуются следующие составы карбюризаторов: 1) 90—95% полукокса; 5—10% ацетата бария; 2) 78—80% полукокса, 10—15% древесного угля; 5—10% ацетата бария.
Свежеприготовленный карбюризатор действует слишком активно. Для цементации пользуются смесью, состоящей из 20—
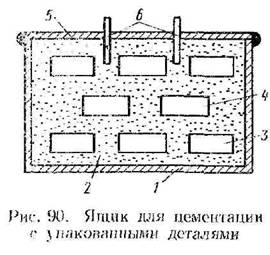
что является вполне достаточным. Увеличение количества активизатора уже не влияет на ускорение цементации.
Применяемый в качестве основной составной части карбюризатора древесный уголь должен быть прочным, определенной зернистости (4—10 мм в поперечнике). При меньшей зернистости древесного угля нарушается циркуляция газов в цементационных ящиках; при большей — уменьшается общая поверхность карбюризатора, что понижает активность процесса. Карбюризатор должен сохранять достаточную прочность, не дробиться и не образовывать пыли, содержать незначительное количество вредных примесей (золы, серы и др.) и давать минимальную усадку при температурах цементации. Сера (при содержании более 0,1%) диффундирует в металл и разъедает поверхность. Карбюризатор должен быть сухим (влажность не более 5—696), так как вода, испаряясь при температурах цементации, влияет на состав газовой среды и замедляет процесс.
Технология цементации. Конструкция цементационных ящиков оказывает большое влияние на продолжительность процесса цементации и качество цементуемых деталей. К цементационному ящику предъявляются следующие требования: 1) форма ящика должна приближаться к форме цементуемых деталей; 2) должен быть обеспечен наиболее быстрый прогрев деталей; 3) рабочее пространство печи должно использоваться эффективно. Для цементации применяют прямоугольные ящики (наибольшие размеры ящика 250x500x300 мм). Ящики изготовляют из стали, чугуна и жаростойких сплавов; стойкость сварных ящиков до 150—200 ч, литых (стальных и чугунных) — 250—500 ч, из жаростойких сплавов — 4000—6000 ч. С целью повышения стойкости цемента-шюнные ящики целесообразно подвергать алитированию. Упаковка деталей в цементационный ящик производится следующим образом (рис. 90).
На дно ящика насыпают слой карбюризатора 2 толщиной 30—40 мм; на него укладывают первый ряд деталей 3. Расстояние между деталями и между деталями и стеной ящика 20—25 мм. На первый ряд деталей насыпают слой карбюризатора толщиной 20— 25 мм, укладывают следующий ряд деталей 4, снова засыпают карбюризатором, и так до полного заполнения ящика. Верхний ряд деталей засыпают слоем карбюризатора толщиной 20—35 мм, При упаковке деталей карбюризатор плотно утрамбовывают, Сверху укладывают лист асбеста, ящик закрывают крышкой 5 и обмазывают глиной. Через отверстия, имеющиеся в крышке, в ящик вставляют два указателя 6, служащие для контроля цементации.
Ящики с упакованными в них деталями сушат на воздухе и затем устанавливают в печь, нагретую до температуры цементации (900—950° С); при этом температура печи снижается. При температуре 780—800° С следует проводить сквозной прогрев ящиков, что обеспечивает более равномерную цементацию. Затем температуру быстро повышают до 900—950° С и выдерживают в зависимости от требуемой толщины слоя: при толщине слоя до 1 мм скорость цементации составляет 0,15 мм/ч; при толщине слоя более 1 мм—0,1 мм/ч.
Ниже приведены данные, характеризующие зависимость толщины слоя от продолжительности выдержки при температуре цементации 920—930° С:
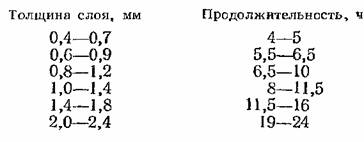
После окончания цементации ящики вынимают из печи и охлаждают на воздухе до температуры не выше 100° С; затем ящики разбирают.
|