Технология термической обработки металловТермическая обработка чугуна и сплавов цветных металлов
Термическая обработка чугуна
Отжиг
Чугун подвергают отжигу, нормализации, закалке и отпуску, а также некоторым видам химико-термической обработки (азотированию, алитированию, хромированию).
Графитизирующий отжиг применяют для получения ковкого чугуна из белого чугуна и для устранения отбела отливок из серого чугуна. Для получения ковкого чугуна используют белый доэвтектический чугун (2,5—3,0% С; 0,5—1,5% 51; 0,3—1,0% Мп; 0,08—0,2% Р; не более 0,12% 5), в котором при отжиге происходит распад цементита с образованием графита — графитизация белого чугуна.
Графитизацию при температурах выше критической можно представить следующим образом:
аустенит и графит.
(рис. 119, а) аустенит в равновесии с графитом имеет состав в точке б, а в равновесии с цементитом — состав в точке в, т. е. аустенит будет химически неоднородным (рис. 119, б и рис. 120). В возникающей системе из трех фаз — аустенита, графита и цементита аустенит не может одновременно находиться в равновесии с цементитом и графитом. Вследствие стремления системы к равновесию из аустенита, пересыщенного в слое, прилегающем к графиту, будет выделяться избыток углерода и включения графита будут расти (см. рис. 120). Но так как при этом аустенит становится ненасыщенным в слое, прилегающем к цементиту, то происходит распад цементита и растворение углерода в аустените, что снова вызывает пересыщение аустенита в слое, прилегающем к графиту, и выделение из него избыточного углерода. Таким образом, распад цементита продолжается до полного его растворения в аустените, после чего между включениями графита и аустенитом состава в точке б (см. рис. 119, б) устанавливается равновесие (см. рис. 120). В результате такого распада образуется хлопьевидный графит (углерод отжига), характерный для структуры ковкого чугуна.
На рис. 121 приведена схема отжига белого чугуна для получения ковкого чугуна. В исходном состоянии белый доэвтекти-ческий чугун имеет структуру, состоящую из перлита, вторичного и эвтектического цементита. При переходе эвтектоидного интервала температур перлит превращается в аустенит, а при повышении температуры до 950—1000° С в аустените растворяется часть вторичного цементита и чугун имеет структуру аустенит и цементит. При выдержке при температуре 950—1000° С происходит распад цементита (эвтектического и вторичного) и образуется структура аустенит и графит. Этот процесс называют первой стадией графитизации.
. И в том и в другом случае будет получаться структура феррит и графит; этот процесс называют второй стадией графитизации. Если вместо ферритного ковкого чугуна требуется, чтобы структура была перлитной или феррито-перлитной, то вторую стадию графитизации совсем не проводят или не доводят до конца и после первой стадии графитизации или после частично проведенной второй стадии охлаждают на воздухе. В первом случае будет получаться структура перлит и графит, во втором — феррит, перлит и графит.
Для сокращения времени отжига белого чугуна применяют следующие методы: модифицирование, предварительную закалку, предварительную низкотемпературную выдержку. Наиболее распространенным элементом, применяемым для модифицирования чугуна, является алюминий, добавляемый в небольшом количестве (0,01—0,02%). Отжиг с предварительной закалкой заключается в том, что белый чугун подвергают закалке с 900— 950° С в воде или масле. При закалке, во время мартенситного превращения, образуются многочисленные микротрещины, в которых наиболее легко зарождаются центры графитизации.
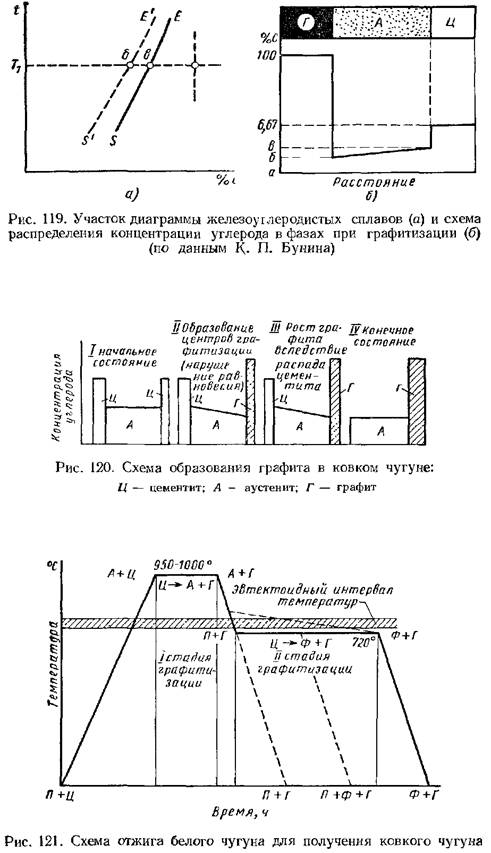
Отжиг с предварительной низкотемпературной выдержкой заключается в том, что белый чугун выдерживают в течение 6— 8 ч при 350—400° С. Число центров графитизации увеличивается, и сокращается время отжига. Механизм влияния низкотемпературной выдержки еще не установлен. Если ковкому чугуну хотят придать одновременно повышенную прочность и пластичность, применяют сфероидизирующий отжиг, в результате которого получается структура зернистого перлита и графита. Используют белый чугун с повышенным содержанием марганца (около 1%). Марганец незначительно удлиняет первую стадию графитизации, но тормозит распад цементита во второй стадии, что позволяет дать выдержку, достаточную для превращения пластинчатого перлита в зернистый.
повторяют несколько раз.
Графитизирующий отжиг применяют также для устранения отбела отливок из серого чугуна, возникающего в их тонких сечениях, или при литье в металлические формы, в связи с чем повышается хрупкость и резко снижается обрабатываемость. При проведении данного отжига отливки нагревают до 850—950° С в течение 2—3 ч (первая стадия графитизации) и охлаждают на воздухе до температуры 20° С или проводят вторую стадию графитизации (2—6 ч). Быстрый распад цементита объясняется повышенным содержанием в серых чугунах кремния (1,5—3%). В результате отжига устраняется отбел и структура становится перлитной, феррито-перлитной или ферритной.
Низкотемпературный отжиг применяют для снятия внутренних остаточных напряжений отливок серого чугуна. Данный отжиг проводят по следующему режиму: медленный нагрев отливок (30—180° С/ч) до 530—620° С, выдержка при этой температуре 3—4 ч (с момента нагрева до заданной температуры наиболее толстого сечения отливки) и медленное охлаждение вместе с печью со скоростью 10—30° С/ч до 300—400° С. В результате такого отжига внутренние остаточные напряжения уменьшаются на 80— 85%. Отжиг при более высоких температурах может вызвать графитизацию эвтектоидного цементита, снижение твердости и прочности чугуна.
Забиваем Сайты В ТОП КУВАЛДОЙ - Уникальные возможности от SeoHammer
Каждая ссылка анализируется по трем пакетам оценки: SEO, Трафик и SMM.
SeoHammer делает продвижение сайта прозрачным и простым занятием.
Ссылки, вечные ссылки, статьи, упоминания, пресс-релизы - используйте по максимуму потенциал SeoHammer для продвижения вашего сайта.
Что умеет делать SeoHammer
— Продвижение в один клик, интеллектуальный подбор запросов, покупка самых лучших ссылок с высокой степенью качества у лучших бирж ссылок.
— Регулярная проверка качества ссылок по более чем 100 показателям и ежедневный пересчет показателей качества проекта.
— Все известные форматы ссылок: арендные ссылки, вечные ссылки, публикации (упоминания, мнения, отзывы, статьи, пресс-релизы).
— SeoHammer покажет, где рост или падение, а также запросы, на которые нужно обратить внимание.
SeoHammer еще предоставляет технологию Буст, она ускоряет продвижение в десятки раз,
а первые результаты появляются уже в течение первых 7 дней.
Зарегистрироваться и Начать продвижение
Стабильность размеров чугунной отливки обеспечивается только в том случае, если после низкотемпературного отжига проводится старение (вылеживание отливок после предварительной обработки на металлорежущих станках перед окончательной обработкой).
|