Технология термической обработки металловТермическая обработка сплавов цветных металлов
АЛЮМИНИЕВЫЕ СПЛАВЫ
Отжиг. Алюминиевые сплавы подвергают трем видам термической обработки: отжигу, закалке и старению. Основными видами отжига являются: диффузионный (гомогенизация), рекристаллизационныи и термически упрочненных сплавов.
Гомогенизацию применяют для выравнивания химической микронеоднородности зерен твердого раствора путем диффузии, т, е. уменьшения дендритной ликвации в слитках. Так как скорость диффузии увеличивается с повышением температуры, а количество продиффундировавшего вещества тем больше, чем длительнее выдержка, то для энергичного протекания диффузии необходимы высокая температура (близкая к температуре линии солидуса) и продолжительная выдержка.
Для выполнения гомогенизации алюминиевые сплавы (слитки) нагревают до 450—520° С и выдерживают при этих температурах от 4 до 40 ч; после выдержки — охлаждение вместе с печью или на воздухе. В результате гомогенизации структура становится более однородной (гомогенной), повышается пластичность, что значительно улучшает последующую деформацию слитка горячей обработкой давлением. Поэтому гомогенизацию широко применяют для деформируемых алюминиевых сплавов.
Для алюминия и алюминиевых сплавов (а также для других цветных металлов и сплавов) рекристаллизационныи отжиг применяют гораздо шире, чем для стали. Это объясняется тем, что такие металлы, как алюминий и медь (используемые в промышленности в чистом виде), а также многие сплавы на их основе, не упрочняются закалкой и повышение их механических свойств может быть достигнуто только холодной обработкой давлением, а промежуточной операцией при такой обработке (для восстановления пластичности) является рекристаллизационныи отжиг. Кроме того, сплавы, упрочняемые закалкой, часто подвергают холодной обработке давлением с последующим рекристаллиза-ционным отжигом для придания требуемых свойств. Температура рекристаллизационного отжига алюминиевых сплавов 300—500° С, выдержка 0,5—2 ч.
Отжиг термически упрочненных сплавов применяют для полного снятия упрочнения, полученного в результате закалки и старения; он проводится при температурах 350—450° С с выдержкой 1—2 ч и последующим достаточно медленным охлаждением (со скоростью не более 30° С/ч), чтобы обеспечить протекание диффузионных процессов распада твердого раствора и коагуляцию продуктов распада.
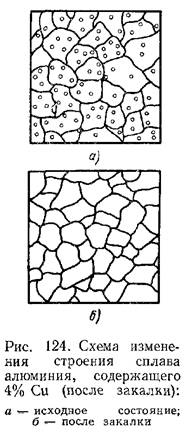
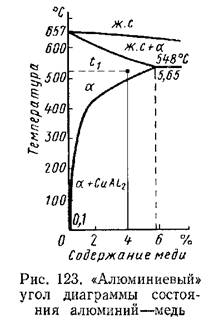
Некоторые элементы, входящие в алюминиевые сплавы, образуют с алюминием ограниченные твердые растворы переменной концентрации, в которых растворимость элементов с понижением температуры уменьшается. На этом и основывается закалка алюминиевых сплавов.
растворяются, и образуется однофазный твердый а-раствор. Быстрым охлаждением (закалка в воде) фиксируется твердый а-раствор (пересыщенный) меди в алюминии (см. рис. 124, б). После закалки прочность сплава несколько повышается, а пластичность не изменяется.
протекают следующие процессы.
При температуре 20° С (естественное старение) и при
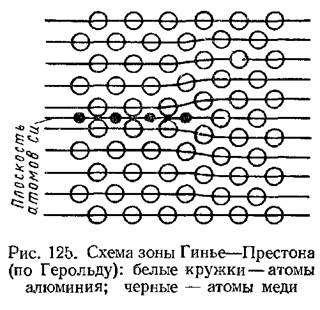
температурах до 100°С (искусственное старение) в пересыщенном твердом растворе возникают области (тонкопластинчатой, дискообразной формы), обогащенные атомами меди, названные зонами Гинье—Престона и обозначаемые Г. П., а для данного начального процесса Г. П. 1. Эти зоны имеют толщину 5—10 А и диаметр 40—100 А. Структура их неупорядоченная, как и твердого раствора. Образование зон Г. П. 1 сопровождается искажением кристаллической решетки (рис. 125), что приводит к повышению механических свойств сплава.
, и их наличие обусловливает максимальную прочность сплава.
. Но выделения 0-фазы не имеют границ раздела с зернами твердого раствора, т. е. когерентно связаны с решеткой алюминия. Таким образом, появление зон Г. П. 1 и Г. П. 2 — это подготовительные стадии к началу распада твердого раствора (выделению избыточной фазы), а образование б-фазы — начало распада твердого раствора (выделение избыточной фазы).
При температурах 200—250° С решетка 0-фазы отрывается от решетки твердого раствора (когерентность полностью нарушается) и оформляется в решетку, соответствующую соединению
(6-фаза).
5. Дальнейшее повышение температуры приводит к коагуляции выделившейся 6-фазы, резкому снижению прочности и повышению пластичности.
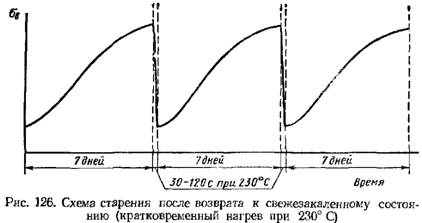


Возврат. В алюминиевомедных сплавах состояние, получившееся в результате естественного или низкотемпературного старения, является неустойчивым. Если такой сплав нагреть до 230— 250° С с короткой (30—120 с) выдержкой, с последующим быстрым охлаждением (в воде), то упрочнение исчезает и сплав по своим свойствам возвращается к свежезакаленному состоянию (рис. 126). Однако после охлаждения естественное старение снова повторяется, и сплав опять упрочняется.
то за это время произойдет
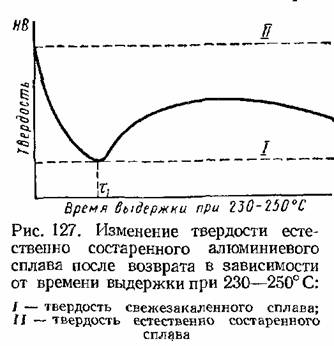
рассасывание зон Г. П., сплав
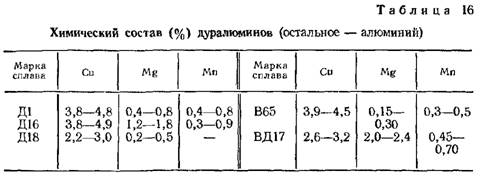
с повышением твердости.

Деформируемые алюминиевые сплавы. Наиболее распространенными деформируемыми алюминиевыми сплавами являются дуралюмины — сплавы алюминия с медью и магнием с добавками марганца (табл. 16).

. Микроструктура дуралюмина после отжига состоит из твердого а-раствора и включений различных фаз (см. рис. 128, а).
(рис. 128, в).
В закаленном состоянии дуралюмины пластичны и легко деформируются. После закалки и естественного или искусственного старения прочность дуралюмина резко повышается (рис. 129). Максимум прочности получается после естественного старения. При искусственном старении сплав упрочняется тем быстрее, чем выше температура старения, но максимум прочности при этом получается более низким.
Забиваем Сайты В ТОП КУВАЛДОЙ - Уникальные возможности от SeoHammer
Каждая ссылка анализируется по трем пакетам оценки: SEO, Трафик и SMM.
SeoHammer делает продвижение сайта прозрачным и простым занятием.
Ссылки, вечные ссылки, статьи, упоминания, пресс-релизы - используйте по максимуму потенциал SeoHammer для продвижения вашего сайта.
Что умеет делать SeoHammer
— Продвижение в один клик, интеллектуальный подбор запросов, покупка самых лучших ссылок с высокой степенью качества у лучших бирж ссылок.
— Регулярная проверка качества ссылок по более чем 100 показателям и ежедневный пересчет показателей качества проекта.
— Все известные форматы ссылок: арендные ссылки, вечные ссылки, публикации (упоминания, мнения, отзывы, статьи, пресс-релизы).
— SeoHammer покажет, где рост или падение, а также запросы, на которые нужно обратить внимание.
SeoHammer еще предоставляет технологию Буст, она ускоряет продвижение в десятки раз,
а первые результаты появляются уже в течение первых 7 дней.
Зарегистрироваться и Начать продвижение
Обработка закаленного дуралюмина при низких температурах задерживает распад твердого а-раствора (—5° С); при —50° С распад не происходит. Обработка холодом дуралюмина дает результаты, противоположные результатам обработки холодом закаленной стали (низкотемпературная обработка которой способствует более полному распаду твердого раствора — аустенита).
Период, при котором после закалки дуралюмина упрочнение не наступает, сравнительно невелик и оставляет 1—6 ч. В это время и должны проделываться все операции холодной деформации (штамповка, высадка, расклепка и т. п.)
(например, для дуралюминов Д16, Д18, ВД17 495—505° С, для дуралюмина Д1 500—510° С, для дуралюмина В65 — 515— 525° С). Указанные температуры нагрева необходимо строго соблюдать при закалке дуралюминов, так как нагрев до температур
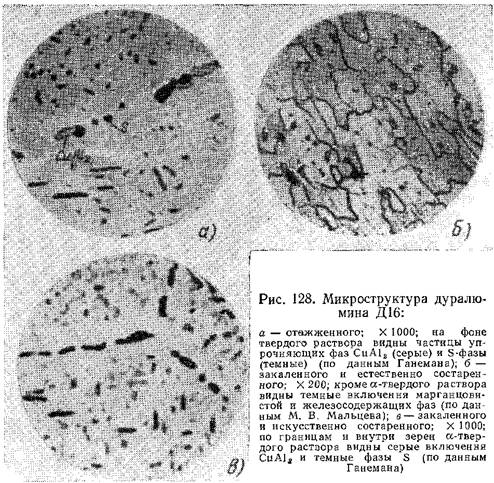
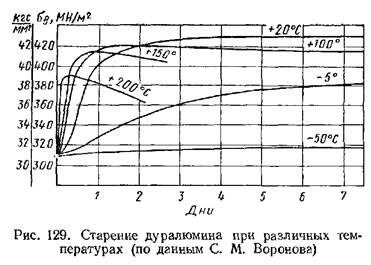
выше или ниже рекомендованного интервала приводит к значительному снижению прочности и пластичности.
Снижение механических свойств дуралюмина при нагреве до температуры выше допустимых пределов связано с оплавлением эвтектики сопровождающимся по границам зерен окислением металла, т. е. происходит пережог. При нагреве до температуры ниже допустимых пределов не произойдет максимального растворения упрочняющих фаз.
Вследствие узкого предела допустимых температур нагрева дуралюминов под закалку применяемые печи должны обеспечивать равномерность нагрева и перепад температур, не превышающий интервала температур закалки. Этим требованиям удовлетворяют соляные (селитряные) ванны и электрические печи с принудительной циркуляцией воздуха.
Нагретые алюминиевые сплавы (после выдержки при температуре закалки) охлаждают в холодной воде с температурой не выше 30—40° С с быстрым их переносом из печи (ванны) в закалочный бак. Такие условия охлаждения необходимы для того, чтобы зафиксировать в сплаве твердый раствор и получить в дальнейшем (при старении) необходимое упрочнение, а также для предотвращения межкристаллитной коррозии, склонность к которой повышается даже при незначительном распаде твердого раствора с выделением избыточных фаз по границам зерен.
Механические свойства наиболее распространенного дуралюмина Д16 после отжига, непосредственно после закалки и после закалки и старения приведены в табл. 17.
Литейные алюминиевые сплавы. Для литейных алюминиевых сплавов используют различные виды термической обработки в зависимости от химического состава сплава и назначения литых
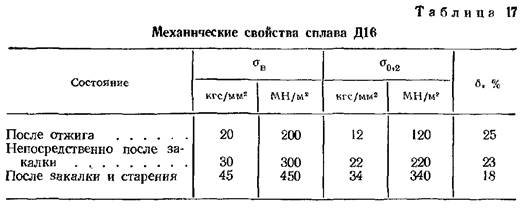
деталей. Виды термической обработки имеют условные обозначения: Т1 — искусственное старение без предварительной закалки; Т2 — отжиг; ТЗ — закалка; Т4 — закалка и естественное старение; Т5 — закалка и частичное (неполное) искусственное старение; Т6 — закалка и полное искусственное старение; Т7 — закалка и стабилизирующий отпуск; Т8 — закалка и смягчающий отпуск.
Термическая обработка литейных алюминиевых сплавов по сравнению с термической обработкой деформированных сплавов имеет ряд особенностей, что объясняется различным химическим составом, а также тем, что у литейных сплавов структура более крупнозернистая, чем у деформированных. Температура нагрева под закалку у литейных сплавов несколько выше, чем у деформированных, и выдерживать отливки при этой температуре надо более длительное время. Это необходимо для того, чтобы растворить интерметаллические соединения, обычно выделяющиеся по границам зерен, и обеспечить уменьшение ликвации сплава. При закалке литейные сплавы выдерживают при температуре нагрева от 2 до 20 ч. Охлаждают литейные сплавы при закалке в холодной и нагретой (50—100° С) воде, а также и в масле.
Для упрочнения литейные алюминиевые сплавы подвергают (так же как и деформируемые) закалке с получением пересыщенного твердого раствора и искусственному старению (по режимам Т5 и Тб) с выделением упрочняющих фаз, а также (в отличие от деформируемых сплавов) только закалке без старения с получением в закаленном состоянии устойчивого твердого раствора.
Для многих сплавов в зависимости от условий работы деталей рекомендуются различные режимы термической обработки; например, для деталей из сплава АЛ9*—режимы Т4, Т5, Т6, Т7, Т8; из сплава АЛ5 ** — режимы Т1, Т5, Т6, Т7; из сплава АЛ20 *** — режимы Т2, Т5, Т7.

в течение 3—5 ч — применяют для крупных деталей большой нагруженности, работающих при повышенных температурах и требующих повышенной пластичности и стабильности геометрических размеров.
|