Технология термической обработки металловМолотовые штампы
Штампы из сталей 5ХНСВ, 5ХНМ, 5ХНВ и 5ХГМ. Для устранения внутренних напряжений, возникающих при ковке, для измельчения зерна, получения однородной структуры и понижения твердости заготовки штампов (кубики) подвергают отжигу или нормализации с высоким отпуском по режиму для данной стали.
На качество штампов и стойкость их в работе влияет термическая обработка — закалка и отпуск штампов. Если термическая обработка штампов проведена неудовлетворительно, то в штампах могут возникать трещины (в процессе термической обработки или после некоторого времени работы). Штампы разрушаются вследствие значительных внутренних напряжений, возникающих при нагреве и охлаждении. Особенно большие напряжения при термической обработке крупных штампов. При нагреве внутренние напряжения возникают в связи с разницей температур в отдельных зонах штампа. Для уменьшения внутренних напряжений нагрев под закалку и отпуск должен производиться с таким расчетом, чтобы получилась минимальная разница между температурой поверхности и температурой сердцевины штампа.
Для предотвращения образования значительных внутренних напряжений от неравномерного нагрева штампы необходимо медленно нагревать до 500—600° С. При дальнейшем повышении температуры нагрев может быть более быстрым. Обычно при нагреве под закалку штампы загружают в печь, имеющую температуру не выше 650° С. При загрузке холодных штампов температура печи понижается и тем в большей степени, чем крупнее штампы.
Для предохранения от окисления и обезуглероживания при нагреве рабочую поверхность штампа засыпают отработавшим карбюризатором, сверху обмазывают шамотной глиной и устанавливают в печь фигурой вверх (рис. 183, а) или фигурой вниз в железную

коробку, в которую насыпают слой отработавшего карбюризатора (рис. 183, б).
Температура закалки штампов 820—880° С (более низкая температура для закалки мелких штампов, более высокая — для крупных). Температуру закалки принимают 840—860° С для стали 5ХНСВ и 820—860° С для сталей 5ХНМ, 5ХНВ, 5ХГМ.
Для штампов с наименьшей стороной (высотой) 250—700 мм (при нагреве в электропечи) принимают выдержку после загрузки в печь 40 мин — 2,5 ч; нагрев до температуры закалки 11—23 ч, выдержку при температуре закалки 2—5,5 ч. После выдержки при температуре закалки штампы для уменьшения напряжений и деформации подстуживают на воздухе до 750—780° С в течение 15—40 мин и охлаждают в масле с температурой не выше 70° С или на воздухе. Более однородная структура получается при охлаждении в масле. Штамп погружают в масло рабочей частью вниз. Во время охлаждения штамп все время находится в подвешенном состоянии. В масле штамп выдерживают до тех пор, пока температура нагретой поверхности штампа не понизится до 200— 150° С. В зависимости от размера (250—700 мм) штампы выдерживают в масле от 30 мин до 2 ч.
После закалки штампы немедленно подвергают отпуску. Отпуск штампов снижает их твердость и уменьшает внутренние напряжения, возникающие в штампах в результате закалки. Закалочные напряжения в штампах бывают настолько велики, что если штамп после закалки оставить без отпуска, то через некоторое время в нем образуются трещины. Если закаленный штамп поместить в печь, нагретую до температуры отпуска (500—600° С), то при быстром нагреве поверхностных слоев и значительной разнице между температурой поверхности и температурой сердцевины в штампе могут возникнуть трещины. Поэтому штампы после закалки помещают в отпускную печь, нагретую до температуры не выше 400° С, а затем нагревают до заданной температуры отпуска. Температура отпуска и твердость после отпуска зависят от стали и размера штампа Более высокая твердость (HRC 40—44) допускается для мелких штампов, в которых деформируемый металл подстывает быстрее. Эти штампы мало деформируются при закалке, поэтому закалку и отпуск можно проводить после окончательной обработки на металлорежущих станках. Средние штампы должны иметь твердость HRC 36—41. Такая твердость позволяет применять комбинированный метод изготовления в следующей последовательности: черновое нарезание фигуры с допуском, термическая обработка, окончательная обработка резанием после термической обработки.
Крупные штампы должны иметь высокую вязкость; их отпускают до твердости HRC 35—38. Сначала закаливают и отпускают кубики, а затем нарезают фигуру. Изношенные штампы обрабатывают резанием без промежуточного отжига, далее вновь проводят термическую обработку. Температуры отпуска и твердость молотовых штампов приведены в табл. 25.
Штампы с наименьшей стороной (высотой) 250—700 мм нагревают в электропечи до температуры отпуска в течение 9—25 ч и выдерживают при температуре отпуска в течение 1,5—5 ч. Так как хвостовая часть штампа должна иметь повышенную вязкость, после общего отпуска производят отпуск хвостовика. Для этого штамп хвостовиком вниз устанавливают на специальную щелевую печь или на печь-плиту. Производят нагрев до появления синего или серого цвета побежалости на рабочей части штампа, что соответствует температуре 250—350° С. Температуры отпуска и твердость хвостовиков приведены в табл. 26.
Для сокращения цикла термической обработки рекомендуется следующий способ закалки штампов. Нагретый до температуры закалки штамп накрывают со стороны хвостовой части герметическим коробом (рис. 184) и в таком виде погружают в масло. При охлаждении масло внутрь короба не проникает, так как этому препятствуют находящиеся в коробе воздух и пары масла. При таком способе охлаждения хвостовик не закаливается, а подвергается нормализации с самоотпуском с получением необходимой
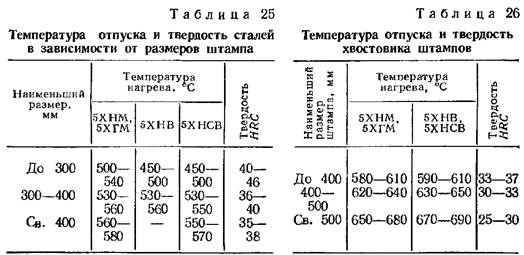
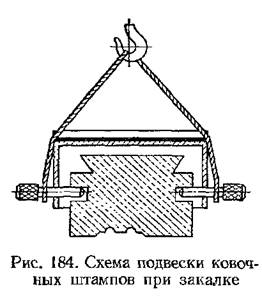
твердости, и поэтому дополнительный отпуск проводить не требуется. Прогрессивным способом, сокращающим цикл термической обработки и улучшающим качество штампов, является способ местной закалки. Штампы нагревают на специальной щелевой газовой печи при установке их фигурой вниз. При таком способе рабочая часть штампа нагревается до температуры закалки; нагрев хвостовика не превышает 450° С, т. е. наблюдается резкое понижение температуры от рабочей к хвостовой части штампа; хвостовик сохраняется мягким. Штампы нагревают на щелевой печи без защитной обмазки. Образующийся тонкий слой окалины (несколько сотых миллиметра) легко снимается с фигуры штампа. После закалки производят отпуск по обычным режимам для рабочей части.
Забиваем Сайты В ТОП КУВАЛДОЙ - Уникальные возможности от SeoHammer
Каждая ссылка анализируется по трем пакетам оценки: SEO, Трафик и SMM.
SeoHammer делает продвижение сайта прозрачным и простым занятием.
Ссылки, вечные ссылки, статьи, упоминания, пресс-релизы - используйте по максимуму потенциал SeoHammer для продвижения вашего сайта.
Что умеет делать SeoHammer
— Продвижение в один клик, интеллектуальный подбор запросов, покупка самых лучших ссылок с высокой степенью качества у лучших бирж ссылок.
— Регулярная проверка качества ссылок по более чем 100 показателям и ежедневный пересчет показателей качества проекта.
— Все известные форматы ссылок: арендные ссылки, вечные ссылки, публикации (упоминания, мнения, отзывы, статьи, пресс-релизы).
— SeoHammer покажет, где рост или падение, а также запросы, на которые нужно обратить внимание.
SeoHammer еще предоставляет технологию Буст, она ускоряет продвижение в десятки раз,
а первые результаты появляются уже в течение первых 7 дней.
Зарегистрироваться и Начать продвижение
При ремонте (возобновлении фигуры) штампы подвергают повторной местной закалке без предварительного отжига. Таким образом, вместо четырех операций, необходимых при объемной
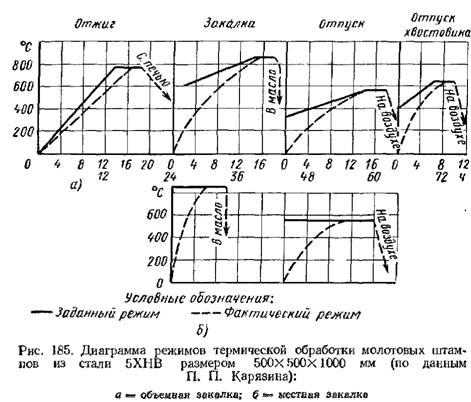
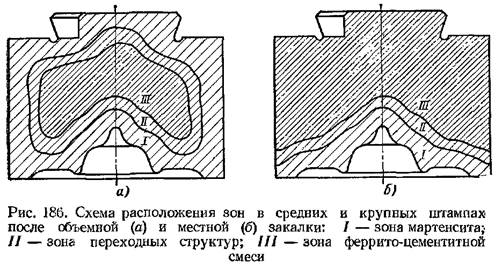
закалке, при местной закалке для получения требуемой твердости рабочей части штампа (рис. 185) нужно только две операции — закалка и отпуск. При надлежащем местном нагреве штампов обеспечивается их глубокая прокаливаемость. Расположение зон микроструктуры (а следовательно, и твердости) после местной закалки более благоприятное по сравнению с расположением зон микроструктуры после объемной закалки (рис. 186). Стойкость штампов после местной закалки выше стойкости штампов после объемной закалки.
Штампы из теплостойких сталей. Предварительная термическая обработка (после ковки) заготовок из теплостойких сталей— отжиг (850—870° С) или отпуск (750—780° С). Вольфрамовые стали лучше отпускать, вольфрамомолибденовые отжигают и отпускают (мелкие поковки). Окончательная термическая обработка — закалка и отпуск.
Температуры закалки и отпуска штампов из теплостойких сталей приведены в табл. 27.
В связи с высокой температурой закалки и длительной выдержкой (крупные штампы) необходима защита от окисления и обезуглероживания. Нагревать при закалке следует с двумя подогревами
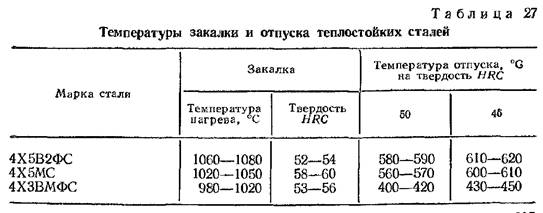
вами; первый — при 700—750° С (выдержка до полного прогрева); второй — при 950—1000° С для сокращения выдержки при окончательном нагреве. Продолжительность выдержки определяют из расчета 30—40 мин на каждые 25 мм наименьшей стороны (высоты) штампа при одном подогреве и 18—25 мин при двух подогревах. После нагрева штамп подстуживают на воздухе до 950—900° С. Охлаждают в масле или водовоздушной смесью (крупные штампы). Небольшие штампы сложной формы можно подвергать изотермической закалке в горячих средах (350—250° С, 20—40 мин). Отпуск проводят немедленно после закалки. Штампы помещают в печь с температурой не выше 400—450° С, выдерживают 1 ч и повышают температуру в печи до заданной. С повышением температуры отпуска улучшается разгаростойкость, но снижается прочность. Крупные и сложные штампы отпускают на твердость HRC 45. Для крупных штампов проводят двукратный отпуск с целью улучшения механических свойств. Температура второго отпуска на 20—25° С ниже температуры первого отпуска.
|