Ультра звуковая сварка пластмасс и металловНекоторые особенности образования сварных соединений металлов и пластмасс
Основные концепции теории твердофазного соединения различных металлов изложены в ряде работ [1 и др. ]. Многочисленные экспериментальные данные, полученные различными авторами, свидетельствуют о резкой интенсификации кинетики схватывания в случае УЗС. При этом разными авторами высказываются различные гипотезы для объяснения этого эффекта. Наиболее интересная, на наш взгляд, модель вакансионного насоса была предложена В. П. Алехиным [2]. Сущность ее состоит в том, что в процессе наложения на свариваемые детали знакопеременных напряжений (напряжение — сжатие) в течение каждого цикла УЗС происходит изменение химического потенциала точечных дефектов. В результате этого возникают периодические пересыщения (при сжатии) и недосыщения (при разгрузке) по вакансиям и соответствующие направленные диффузионные потоки из объема свариваемых материалов к свободным контактным поверхностям в процессе цикла сжатия и, наоборот, от свободных поверхностей в объем свариваемых материалов в процессе циклов разгрузки. При выходе вакансий на свободную поверхность они разрывают насыщенные химические связи и, таким образом, могут являться активными центрами схватывания.
В процессе цикла разгрузки и появления растягивающих напряжений вакансии уходят со свободной поверхности в объем свариваемого материала, что также приводит к разрыву насыщенных химических связей на свободной поверхности.
Таким образом, сущность модели вакансионного насоса состоит в периодическом прокачивании направленного диффузионного потока точечных дефектов, что позволяет резко интенсифицировать кинетику схватывания. Точечные дефекты, в частности вакансии, являются активными центрами твердофазного взаимодействия в силу действия следующих факторов. Во-первых, они, как и дислокации, являются источниками и носителями свободных ненасыщенных связей. Во-вторых, концентрация вакансий на несколько порядков превышает концентрацию дислокаций в кристаллах. В-третьих, вакансии являются основным фактором, лимитирующим скорость протекания диффузии, т. е. процесса объемного взаимодействия. В-четвертых, концентрация вакансий в приповерхностных слоях всегда намного выше, чем в объеме материала, поскольку поверхность является практически бесконечным источником и стоком точечных дефектов в кристалле. Направленный поток вакансий при этом существенно интенсифицирует кинетику гетеродиффузии и направленного массопе-реноса .
Эффект резкой интенсификации кинетики схватывания и увеличения скорости диффузии при УЗС подтвержден с помощью исследования зоны сварного соединения на сканирующем электронном микроскопе УХА-УЗ с локальным рентгеновским микроанализатором.
Из рассмотрения зоны сварки (рис. 1.16) видно, что области объемного взаимодействия представляют собой фактическую зону интенсивного взаимного перемешивания обоих свариваемых металлов. Для структуры в зоне сварки, по сравнению с основным
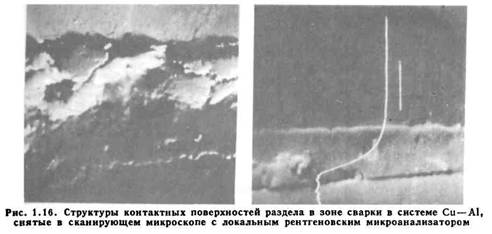
материалом, характерна турбулентность. Причем это свойственно периферийным областям зоны сварки, где существуют максимальные относительные перемещения свариваемых материалов.
Результаты рентгеноспектральных исследований образцов соединения меди с алюминием (рис. 1.16), Тi с АМц и Сu + АМц показывают, что интерметаллидных фаз в зоне контакта нет, поскольку концентрационные кривые взаимного распределения элементов в зоне контакта имеют обычный традиционный вид с нарастанием концентрации одного из элементов от 0 до 100 %. Кривые не имеют горизонтальных ступенек, которые указывали бы на существование интерметаллидных прослоек; очевидно, прослойки не успевают образоваться за столь короткое время сварочного цикла. Это является одним из принципиальных преимуществ УЗС перед другими видами сварки в твердой фазе.
Представляло также интерес исследовать закономерности контактной микродеформадии материалов в зоне УЗС, поскольку, как известно, именно пластическая деформация материалов на всех трех стадиях твердофазной топохимической реакции определяет кинетику образования равнопрочного сварного соединения. В частности, на первой стадии именно за счет контактной микродеформации и смятия микровыступов образуется физический контакт, т. е. свариваемые материалы сближаются до расстояния межатомного взаимодействия. На второй (активационной) стадии за счет выхода структурных дефектов (дислокаций и вакансий) на контактную границу раздела образуются ненасыщенные химические связи, способные вступать во взаимодействие с образованием прочного сварного соединения. На третьей (релаксационной) стадии структурные дефекты, образующиеся при пластической деформации, интенсифицируют кинетику объемного диффузионного взаимодействия. Таким образом, все стадии твердофазного соединения контролируются кинетикой микродеформации на контактных поверхностях раздела свариваемых материалов.
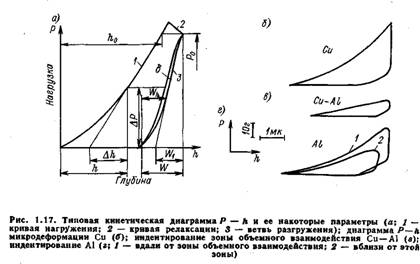
При этом необходимо подчеркнуть, что физические закономерности пластической деформации поверхностных слоев свариваемых материалов резко отличаются в структурном и энергетическом отношении от аналогичных закономерностей деформации внутренних объемных слоев материала [2]. Поэтому существующие в литературе данные по указанным закономерностям для объемных слоев материала нельзя использовать для изучения кинетики УЗС и необходимо привлекать принципиально новые методы для изучения контактной микродеформации при сварке.
Одним из таких методов является новый метод микромеханических испытаний материалов с использованием прибора УПМ-1 (ИМЕТ) и регистрацией кинетики непрерывного вдавливания индентора в координатах: непрерывное изменение нагрузки при микровдавливании (Р, r ) — непрерывное изменение глубины отпечатка, т. е. глубины деформированного слоя h [1, 2]. Данный метод дал возможность точного экспериментального исследования изменения некоторых деформационных свойств свариваемых материалов. Типовая диаграмма микромеханических испытаний в координатах приведена на рис. 1.17, а (6 — ширина петли гистерезиса).
Методика проведения испытаний на кинетическое микровдавливание была принята следующая: испытывались те же самые металлографические поверхности образцов, которые исследовались на сканирующем электронном микроскопе. Отпечатки ставились на линии, расположенной под углом 60° к поверхности раздела свариваемых материалов таким образом, чтобы на зону основного 1 и 2-го материалов и зону диффузионного объемного взаимодействия попало несколько отпечатков: не менее четырех — в основном материале и не менее двух — в зоне диффузионного
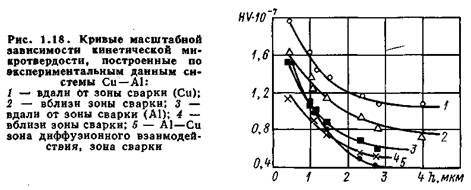
взаимодействия. Время выдержки под нагрузкой составляло 15 с. Полученные экспериментальные данные для сочетания Си — А1; Си —Си; А1 — А1 приведены на рис. 1.17, б. Из экспериментальных кривых видно, что полученные на сканирующем электронном микроскопе данные полностью коррелируются с закономерностями микродеформации и деформационного упрочнения в зоне УЗС.
Забиваем Сайты В ТОП КУВАЛДОЙ - Уникальные возможности от SeoHammer
Каждая ссылка анализируется по трем пакетам оценки: SEO, Трафик и SMM.
SeoHammer делает продвижение сайта прозрачным и простым занятием.
Ссылки, вечные ссылки, статьи, упоминания, пресс-релизы - используйте по максимуму потенциал SeoHammer для продвижения вашего сайта.
Что умеет делать SeoHammer
— Продвижение в один клик, интеллектуальный подбор запросов, покупка самых лучших ссылок с высокой степенью качества у лучших бирж ссылок.
— Регулярная проверка качества ссылок по более чем 100 показателям и ежедневный пересчет показателей качества проекта.
— Все известные форматы ссылок: арендные ссылки, вечные ссылки, публикации (упоминания, мнения, отзывы, статьи, пресс-релизы).
— SeoHammer покажет, где рост или падение, а также запросы, на которые нужно обратить внимание.
SeoHammer еще предоставляет технологию Буст, она ускоряет продвижение в десятки раз,
а первые результаты появляются уже в течение первых 7 дней.
Зарегистрироваться и Начать продвижение
Если сравнить диаграммы Р — h , снятые в зонах основного материала, с зоной диффузионного взаимодействия, т. е. непосредственно в очаге сварки, то видно, что диаграммы по внешнему виду резко различаются.
Более пологий характер ветви нагружения, по сравнению с диаграммами на других позициях, свидетельствует о значительно меньшей твердости и плотности зоны шва УЗС по сравнению с основными материалами. Таким образом, эти данные полностью подтверждают турбулентный (вихревой) характер деформации материала под сварочным наконечником, приводящий к разрыхлению и уменьшению плотности металла сварного шва. Количественные различия по значениям твердости Я = 37,84 Р/h2 представлены на рис. 1.18, которые получены путем обработки экспериментальных диаграмм, приведенных на рис. 1.17, б. Из рисунка видно, что значение твердости по Виккерсу (НУ) при h = 2,5 мкм составляет 47 непосредственно в зоне шва А1 — Си, в то время как твердость А1 составляет 68, а Си — 116.
(см. рис. 1.17, а) оценивалась по формуле
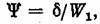
— ширина петли гистерезиса при разгружении и повторном нагружении; W — параметр кинетической диаграммы. Р — к.
, измеренной по диагонали остаточного отпечатка в зоне сварного шва и в основном материале,
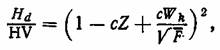
— нормальная деформация на контуре круглого отпечатка, равная

— коэффициенты Пуассона и модули Юнга материала и индентора соответственно.
тогда
= 1,73; 1,84; 2,22; 2,48; 3,6 для кривых 1,2, 3, 4, 5
соответственно, что действительно свидетельствует о более интенсивном деформационном упрочнении материала по кривой 2 по сравнению с кривой 1, кривой 5 по сравнению с 1 и кривых 4, 5 по сравнению с 3 и 4.
— показателя интенсивности проявления масштабной
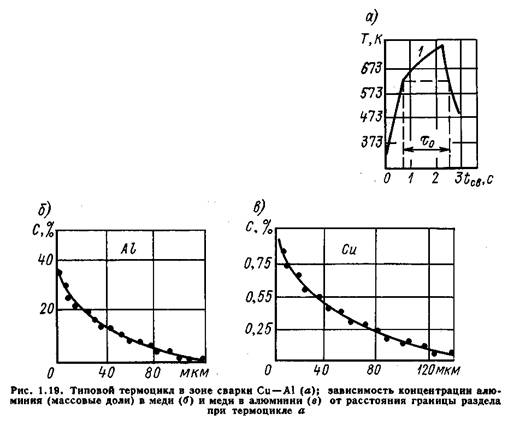
интенсивности
нарастания кривых НV = f (h ) при уменьшении к и др. Варьируя параметрами ультразвукового поля, можно получить уплотнение структуры в зоне сварки.
Определение коэффициентов диффузии в паре Сu —А1 было проведено и на базе измерительных комплексов. При сварке температуру контролировали с помощью хромель — алюминиевых термопар диаметром 0,2 мм, запрессованных непосредственно в зону сварки. Запись термоциклов осуществляли на осциллографе. Типовая осциллограмма приведена на рис. 1.19.
После ультразвуковой сварки образцы разрезали по зоне сварки и проводили рентгеновский микроанализ с помощью прибора МС-46 фирмы КАМЕКА. Распределение концентрации С (х ) определяли по глубине диффузионной зоны в чистом металле от границы раздела. Вводились поправки на поглощение, атомный номер и флуоресценцию по программе 2АР (6—5) из стандартного математического обеспечения сканирующего микроскопа — микроанализатора КАМЕБАКС (число выводимых на печать знаков после запятой было увеличено до 5). Локальность метода составляла 0,9—1,3 мкм, а чувствительность — 0,08— 1, % от содержания элемента.
Одной из методических трудностей определения С (х ) является правильная оценка фона, который появляется из-за намазывания при изготовлении шлифа одного материала на другой. При незначительном удалении от границы раздела свой вклад в фон вносят также отраженные электроны. У самой же границы раздела возникают трудности интерпретации результатов из-за конечного размера зонда и флуоресцентного возбуждения одного элемента другим. Чтобы исключить влияние этих факторов, применялась следующая методика: шлифы образцов пары Сu —А1 с оптическим плотным контактом и не сваренные ультразвуком служили для измерения фона. Измерение фона проводили при тех же параметрах, что и сваренных ультразвуком образцов: шаге и направлении движения зонда, ускоряющем напряжении и силе тока и др. Полученные кривые С (х ) графически вычитались из суммарных кривых, измеренных на изучаемой диффузионной паре.
На полученных таким образом кривых С (х ) (рис. 1.19, б и в) одна из крайних точек (правая) определялась чувствительностью метода, другая — около границы раздела — размерами зонда. Чтобы избежать ошибок, возникающих в связи с последним обстоятельством, обработку кривых С (х ) вели, отступив от границы на расстояние 10 мкм. Отметим, что значения С при х = 0 должны соответствовать растворимости одного элемента в другом, что, как следует из рис. 1.19, б и в и диаграмм состояния для пары Сu —А1, в данном эксперименте соблюдалось.
При определении коэффициентов диффузии по концентрационным кривым, приведенным на рис. 1.19, видно, что мы имеем дело с неизотермическим тепловым процессом, т. е. коэффициент диффузии Д зависит от времени t .
Таким образом, после ультразвуковой сварки Сu —А1 были получены следующие коэффициенты диффузии: меди в алюминии
— длина волны звука для соответствующей температуры) запрессовывались цилиндры диаметром 1,5 мм на различных расстояниях от свободного конца. После предварительного отжига при 420—450 °С в течение 1 ч, необходимого для образования диффузионного соединения между металлами, образцы подвергались ультразвуковому воздействию при



Возвращаясь к основным силам, действующим в зоне сварки, необходимо остановиться на следующем.
. Тенденция к повышению амплитуды колебаний сварочного наконечника предопределялась стремлением увеличить проскальзывание свариваемых поверхностей и интенсифицировать на них процессы внешнего трения (табл. 1.5, тип соединения 1).
. Такой режим должен был бы обеспечить образование более равновесной, чем в рассмотренном выше случае, структуры в силу более благоприятных условий для диффузии в неразрушающихся зонах схватывания.
Исследованы процессы образования сварных соединений такого типа на алюминии и меди. Следует отметить, что использование принципиально новых режимов сварки позволило получить соединения, в микроструктуре которых не обнаружено следов износа и больших пластических течений металла. Такие соединения обладают лучшими прочностными свойствами. Сравнение прочности соединений из меди толщиной 1,0 + 1,0 мм (тип соединения 2) приведено в табл. 1.5. Разрушение этих соединений при испытаниях на срез происходит в большинстве случаев путем вырыва сварной точки. Прочность соединений при испытаниях на отрыв составляет до 50 %.
Сервис онлайн-записи на собственном Telegram-боте
Попробуйте сервис онлайн-записи VisitTime на основе вашего собственного Telegram-бота:
— Разгрузит мастера, специалиста или компанию;
— Позволит гибко управлять расписанием и загрузкой;
— Разошлет оповещения о новых услугах или акциях;
— Позволит принять оплату на карту/кошелек/счет;
— Позволит записываться на групповые и персональные посещения;
— Поможет получить от клиента отзывы о визите к вам;
— Включает в себя сервис чаевых.
Для новых пользователей первый месяц бесплатно.
Зарегистрироваться в сервисе
Удельная прочность сварного соединения остается постоянной при любом времени сварки, а прочность соединения растет за счет увеличения числа зон схватывания. В конце концов они заполняют всю площадь полированного пятна, сливаются друг с другом и образуют сплошное соединение.
свариваемого металла, а амплитуда колебаний сварочного наконечника не превышает тех, которые вызывают относительное проскальзывание свариваемых деталей, являются более целесообразными.
Таким образом, основным условием получения сварных соединений, обеспечивающим высокие прочностные характеристики,
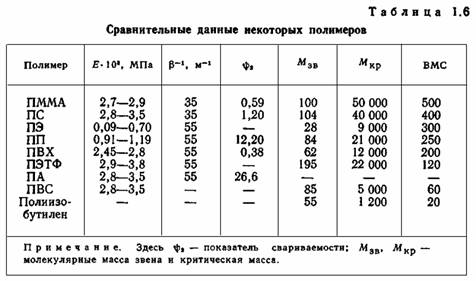
равновесную структуру при минимальных энергетических затратах, является сдвиг энергетического спектра движения сварочного наконечника в сторону увеличения колебательных напряжений, циркулирующих в зоне сварки. Серьезным ограничением механизма образования сварного соединения являются поверхностные пленки. Износ пленок (механоабразивный , физико-химический) является необходимым условием образования сварных соединений при УЗС.
Практически изучение физико-химических явлений, связанное с образованием сварного соединения полимеров и интенсивным вводом энергии ультразвука в зону сварки, находится в начальной стадии.
Рядом исследователей высказаны гипотезы, которые в какой-то мере представляют интерес и задевают комплекс явлений, свойственных процессу УЗС полимеров [6, 8, 9 и др.]. Критический анализ этих концепций дан в работе [6]. В частности, там показано, что существующие представления о механизме образования сварного соединения далеко не полны, односторонни, противоречивы. С этим можно согласиться. Основным вопросом исследователей являлся, как правило, поиск показателя свариваемости полимеров. В качестве таких показателей в свое время предлагали модуль упругости Е, коэффициент затухания р и т. п. Сравнительные данные для некоторых полимеров приведены в табл. 1.6. Такой подход является, на наш взгляд, малоперспективным, хотя бы потому, что он является в значительной мере условным. Действительно, почему при исследовании механизма сварки металлов и не пытаются найти какой-то обобщенный критерий свариваемости?
Более серьезной является постановка вопроса о свариваемости как о процессе энергетическом. Для того чтобы образовалось сварное соединение, надо свариваемые материалы довести до вязкотекучего состояния, т. е. надо ввести определенное количество энергии. Специфика УЗС полимеров в отличие от тривиального случая нагрева теплотой, например горячим воздухом, клином и т. п., заключается в том, что источник энергии и ее преобразование выступают в виде ультразвуковых колебаний сварочного наконечника свариваемых материалов, опоры, т. е. энергии внешнего и внутреннего трения.
Анализ литературы [6, 8] показывает, что наиболее спорным является положение о значимости внешнего и внутреннего трения в механизме преобразования энергии. Из полученных нами экспериментальных данных следует, что в зависимости от свойств свариваемых материалов механизм преобразования энергии трансформируется так: при сварке полимеров роль внутреннего трения существенно повышается или становится доминирующей (например, полиэтилен). Исключить выделение энергии в процессе внешнего трения даже при сварке мягких полимеров, как это предложено исследователями [6], нельзя исходя из следующих соображений.
Движение сварочного наконечника относительно свариваемого материала — удар — вызывает его деформацию. Возврат материала в исходное положение без потерь возможен только при условии идеальных упругих свойств свариваемого материала, но такому материалу не свойственен и механизм внутреннего трения. Если учесть, что удар является классической разновидностью внешнего трения, то оснований для противоречивых толкований нет. Важным является то обстоятельство, что с энергетических позиций механизм свариваемости полимеров надо рассматривать как способность материала поглотить энергию ультразвука. В общем случае можно принять, что для достижения полимером вязкотекучего состояния нужна энергия

— толщина и площадь зоны сварки.
Эта энергия должна выделяться в зоне сварки, что является основным условием образования сварного соединения. Несмотря на внешнюю тривиальность такого утверждения, оно является ответом на многочисленные вопросы относительно свариваемости тех или иных полимеров. Например, трудности со сваркой фторо-пласта-4 можно объяснить именно этим обстоятельством. Сравнительно высокая температура его плавления и, как следствие, необходимость значительного количества энергии, это с одной стороны, с другой — крайне низкий коэффициент внешнего трения, низкая температура, при которой исчезают в нем гармонические колебания и нарушается механизм тепловыделения в результате процессов внутреннего трения.
Однако ни в коем случае нельзя полагать, что поглощение энергии при УЗС полимеров должно идти только за счет потерь внутреннего трения. Увеличение коэффициента потерь при этом ведет к резкому затуханию ультразвуковых колебаний в зоне сварки и снижению эффективности механизма внешнего трения, поскольку на эффект преобразования энергии работает весь объем зоны сварки. В этом отношении примером может служить полистирол.
Таким образом, с позиций энергетики процесса ясно, что энергии ультразвука, выделяющейся в зоне сварки, должно быть достаточно для образования сварного соединения, но перераспределение энергии от процессов внешнего и внутреннего трения определяется, по существу, свойствами свариваемого материала,.
Однозначных представлений о физико-химических явлениях, происходящих непосредственно в зоне сварки, в настоящее время нет. Анализируя литературу, нужно признать, что реологические концепции, изложенные в работе К. И. Зайцева и Л. Н. Мацук являются наиболее работоспособными. При этом необходимо обратить внимание на следующие особенности образования сварного соединения полимеров.
Температура свариваемых поверхностей достигает, как правило, температуры вязкотекучего состояния. Материал находится в знакопеременном механическом поле колебаний. В плоскостях раздела полимера, находящегося в вязкопластическом состоянии, идет интенсивное перемешивание микрообъемов контактирующих слоев. Не исключено насосное действие поверхности источника ультразвука [6]. В любом случае, если поверхности свариваемых материалов находятся в состоянии расплава, процесс УЗС полимеров аналогичен сварке плавлением.
При температурах в зоне сварки ниже температуры текучестиг образование сварных соединений обусловлено диффузионными процессами, которые интенсифицируются УЗС колебаниями. Образование сварного соединения при УЗС идет, как правило, без разложения материала — деструкции, путем перемещения сегментов макромолекул. Сегмент является основной структурной единицей, связывающей основные физико-химические и морфологические свойства полимеров и, в частности, молекулярную массу, температуру стеклования и текучести. Можно сделать предположение, что величина сегмента в какой-то степени может служить показателем свариваемости полимеров [17].
|