Практическая вибродиагностика и монтиторингОрганизация системы ТО предприятия.
Формы технического обслуживания оборудования.
В различных отраслях промышленности эксплуатационные затраты составляют от 6 до 18% стоимости конечной продукции (см. рис. 3 — 03). Их величина бывает сравнима с прибылью предприятия, особенно в области транспорта, в том числе трубопроводного транспорта нефти и газа.
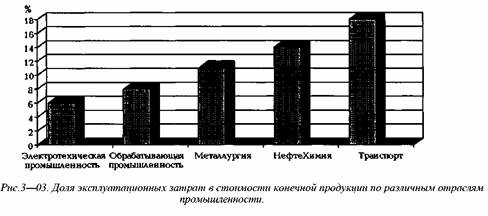
Опыт показывает, что эксплуатационные затраты являются одной из наиболее регулируемых статей затрат предприятия, и снижение эксплуатационных затрат в итоге повышает производительность. Последствия нестабильной работы оборудования проявляются в срыве производственной программы, ухудшении качества и, что самое важное, уменьшении прибыли. Важнейшим резервом снижения эксплуатационных затрат, обеспечения безопасности персонала и сохранности оборудования является совершенствование структуры технического обслуживания оборудования предприятий.
Применяемые в настоящее время виды технического обслуживания оборудования описаны ниже.
Реактивное ("реагирующее") техническое обслуживание — такой метод обслуживания, при котором ремонт или замена оборудования производится только в том случае, когда оно выходит из строя или вырабатывает свой ресурс. Реактивное ("реагирующее") обслуживание имеет следующие недостатки: возможность внеплановых простоев из —з а внезапных отказов оборудования и дорогостоящий и продолжительный ремонт из —за серьезности и обширности дефектов. Кроме того, имеется вероятность внезапного отказа нескольких различных агрегатов одновременно, вследствие чего необходимость в ремонтных работах может превысить возможности ремонтной службы.
Планово — профилактическое техническое обслуживание (в дальнейшем ППР) — такой метод обслуживания, основой которого является плановое периодическое проведение профилактических работ различного объема на оборудовании, т.е. составление и соблюдение календарного графика выполнения через строго определенные интервалы времени работ по профилактическому ремонту (текущему, среднему или капитальному). Достоинством такого метода, по сравнению с реактивным обслуживанием, является резкое снижение вероятности внезапного отказа оборудования. Недостатком планово — профилактического обслуживания является проведение "излишних" ремонтов, т.е. ремонтов фактически исправного оборудования, и, как следствие, излишний рост эксплуатационных затрат.
Достижения в разработке контрольно — измерительной аппаратуры обеспечили возможность не только выявлять состояние агрегата путем измерения ряда его технических параметров, но и на основе анализа изменений измеренных параметров предсказывать необходимость и планировать сроки проведения ремонта, т.е. проводить ремонт только тех агрегатов, где он необходим. Такой вид обслуживания называется "предупредительным", или обслуживанием по фактическому техническому состоянию (в дальнейшем ОФС). Достоинством такого метода обслуживания является минимизация ремонтных работ (исключение ремонта бездефектных узлов) и увеличение на 25...40% межремонтного ресурса по сравнению с ППР. Серьезным недостатком такого вида обслуживания может быть ситуация, когда необходимость в проведении ремонтных работ на нескольких
агрегатах одновременно превысит возможности ремонтной службы.
Проактивное техническое обслуживание (в дальнейшем ПАО) — подход, направленный на снижение общего объема требуемого технического обслуживания и максимизацию срока службы оборудования (т.е. в идеале — создание "вечного" агрегата, не требующего технического обслуживания) путем систематического устранения источников дефектов, приводящих к преждевременному выходу оборудования из строя. Другими словами, по результатам обобщения наиболее часто встречающихся дефектов, выявляемых в процессе работы оборудования, проводится анализ и определение причин их возникновения и влияния на межремонтный интервал, а затем принимаются меры по недопущению возникновения этих дефектов. В частности, производится постоянный анализ работы ремонтного персонала и выявляются недостатки работы той или иной бригады, проявляющиеся на группе агрегатов (например, некачественная сборка, центровка или балансировка), анализ работы ремонтного производства с выявлением недостатков ремонтных технологий (например, технологии изготовления подшипников скольжения), анализ оснащенности (например, отсутствие оснастки по нагреву подшипников качения при монтаже), конструктивные изменения (например, применение износостойких материалов) и др
Характерные особенности влияния различных подходов к техническому обслуживанию на производственный процесс и межремонтные интервалы представлены в таблице 3 — 01.
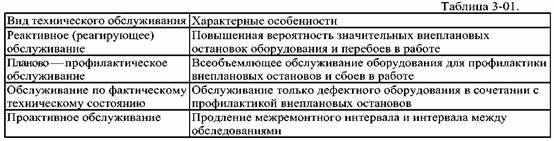
В целях обеспечения стабильной работы оборудования наиболее прогрессивные предприятия перестраивают тактику технического обслуживания: от ремонта вышедшего из строя оборудования к недопущению выхода его из строя (отказа). При этом уменьшаются эксплуатационные затраты и внеплановые остановки производства. Такой прогрессивный подход называется обеспечение надежности механического оборудования (в дальнейшем ОНМО). Стратегия ОНМО направлена на обеспечение надежной работы агрегата или его узлов в течение предполагаемого срока службы. ОНМО представляет собой комбинированную стратегию, объединяющую проактивное обслуживание, обслуживание по фактическому состоянию, планово-профилактическое обслуживание и реактивное обслуживание.
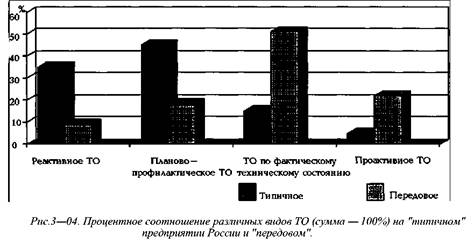
На рис. 3 — 04 отображена такая комбинация различных видов ТО, обычно сосуществующих на любом промышленном предприятии, причем каждая пара столбцов соответствует долям этого ТО в общем объеме работ ремонтной службы. Доли различных видов ТО определяются минимизацией затрат на производство продукции. Разница между типичным предприятием и предприятием, реализующим программу ОНМО, очевидна.
Забиваем Сайты В ТОП КУВАЛДОЙ - Уникальные возможности от SeoHammer
Каждая ссылка анализируется по трем пакетам оценки: SEO, Трафик и SMM.
SeoHammer делает продвижение сайта прозрачным и простым занятием.
Ссылки, вечные ссылки, статьи, упоминания, пресс-релизы - используйте по максимуму потенциал SeoHammer для продвижения вашего сайта.
Что умеет делать SeoHammer
— Продвижение в один клик, интеллектуальный подбор запросов, покупка самых лучших ссылок с высокой степенью качества у лучших бирж ссылок.
— Регулярная проверка качества ссылок по более чем 100 показателям и ежедневный пересчет показателей качества проекта.
— Все известные форматы ссылок: арендные ссылки, вечные ссылки, публикации (упоминания, мнения, отзывы, статьи, пресс-релизы).
— SeoHammer покажет, где рост или падение, а также запросы, на которые нужно обратить внимание.
SeoHammer еще предоставляет технологию Буст, она ускоряет продвижение в десятки раз,
а первые результаты появляются уже в течение первых 7 дней.
Зарегистрироваться и Начать продвижение
Остановимся подробнее на основных видах технического обслуживания оборудования.
|